Understanding Pump Seals: Essential Insights for Businesses
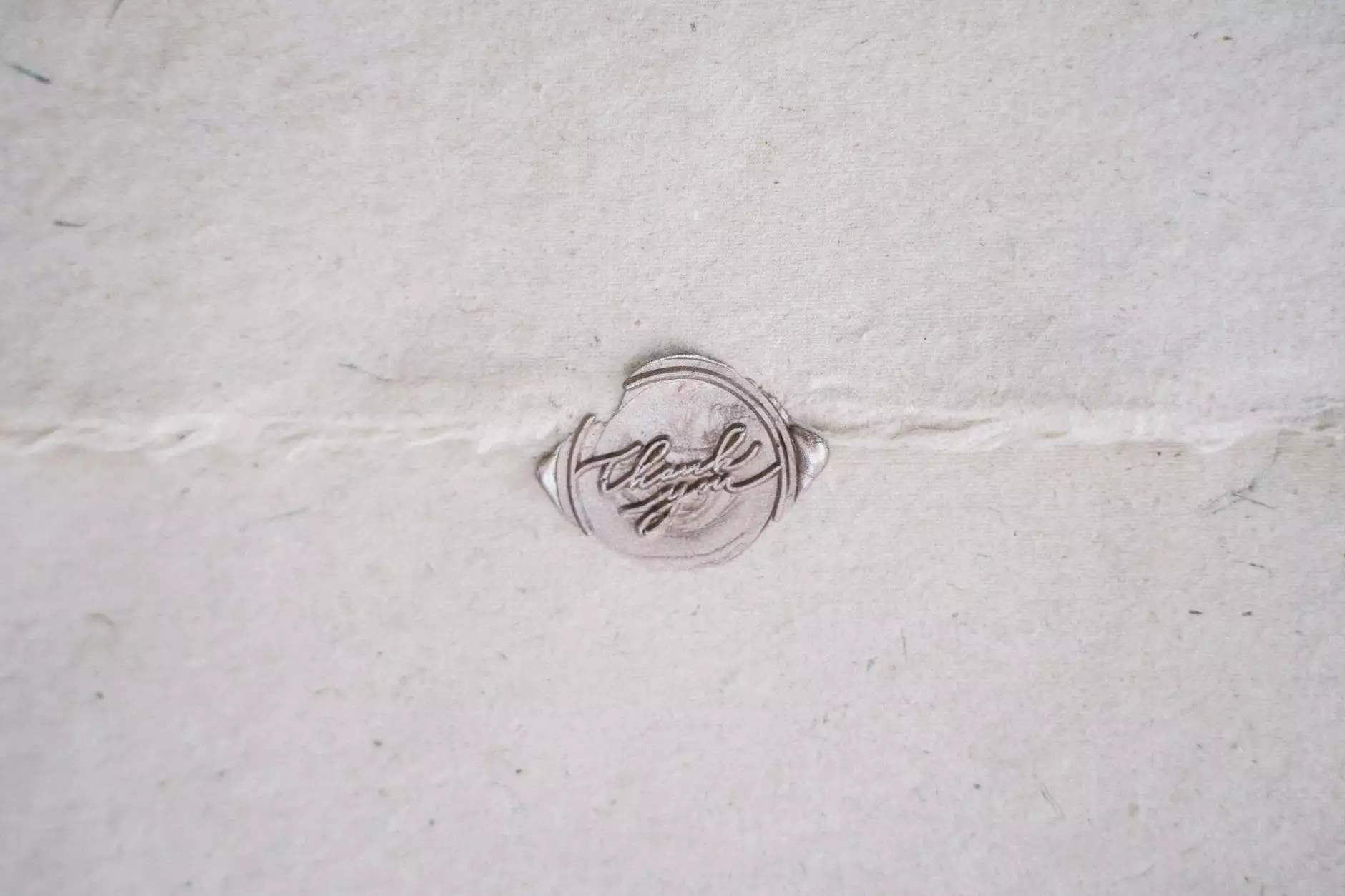
Pump seals play a critical role in many industries by preventing leakage, maintaining pressure, and ensuring operational efficiency. Whether you're involved in auto repair, farm equipment repair, or structural engineering, understanding the importance of pump seals can greatly benefit your business. This article delves into the fundamentals of pump seals, their various types, applications, and best practices for maintenance and selection.
The Importance of Pump Seals in Today’s Industries
In modern businesses, pump seals are indispensable components found in numerous mechanical systems. Their primary function is to prevent the leakage of fluids in pumps and enhance the overall efficiency of operations. Failure to maintain or properly install pump seals can lead to significant operational challenges, including:
- Fluid Leakage: This not only affects the machinery but can also lead to environmental concerns.
- Increased Downtime: Degraded seals may necessitate repair or replacement, causing interruptions in service or production.
- Operational Costs: Poorly functioning seals can lead to increased energy consumption and wastage of resources.
Types of Pump Seals
Understanding the different types of pump seals and their applications is crucial for selecting the right seal for your needs. Here are the most common types:
1. Mechanical Seals
Mechanical seals are widely used in many industries due to their ability to provide an effective seal under varying conditions. They consist of two flat surfaces that are pressed against each other to create a seal. Their advantages include:
- Durability: They can withstand high pressure and temperature changes.
- Minimized Leakage: Mechanical seals are known for their effective sealing capabilities.
2. Gasket Seals
Gasket seals are used to fill spaces between two surfaces to prevent leakage. These are commonly found in auto repair and structural engineering. Gaskets are made from various materials, including rubber and metal composites, and are chosen based on the operating conditions. Key benefits include:
- Versatility: Gasket seals can be tailored to fit different sizes and shapes.
- Cost-Effectiveness: They are generally less expensive than mechanical seals.
3. Packing Seals
Packing seals utilize compressed material, typically in the form of rings, to provide a seal around rotating shafts. Their applications are diverse, spanning from pumps to valves. The advantages of packing seals are:
- Easy Maintenance: They can often be adjusted on-site without needing full disassembly.
- Adaptability: Suitable for varying speeds and pressures.
Choosing the Right Pump Seal: Key Considerations
Selecting the appropriate pump seal involves considering several critical factors to ensure optimal performance:
- Operating Conditions: This includes temperature, pressure, and the type of fluid being sealed. Understanding these parameters will help in selecting the right material and type of seal.
- Seal Material: The material of the seal should be compatible with the fluid to minimize chemical reactions.
- Installation Space: Some seals require more space than others; thus, it's essential to consider the dimensions available for installation.
- Cost vs. Performance: While it may be tempting to choose the least expensive option, balancing cost and performance is crucial for long-term success.
Maintenance of Pump Seals: Best Practices
Proper maintenance of pump seals can extend their lifespan and improve operational efficiency. Here are some best practices:
1. Regular Inspections
Conduct periodic inspections of seals to detect any signs of wear and tear, such as leaks or misalignment. Early detection can prevent costly downtimes.
2. Proper Installation
Ensure that seals are installed correctly as per manufacturer specifications. Improper installation can lead to premature failure.
3. Use Appropriate Lubricants
Apply the right amount and type of lubricant, as specified by the seal manufacturer, to reduce friction and wear.
4. Train Personnel
Educate your team on the importance of pump seals and standard maintenance procedures. Knowledgeable personnel can identify issues early and take appropriate actions.
Common Applications of Pump Seals in Various Industries
Pump seals are crucial across several sectors. Below are common applications highlighting their significance:
Auto Repair
In the auto repair industry, pump seals are essential components in various systems, such as cooling systems, oil pumps, and fuel pumps. Proper functioning of seals ensures that fluids remain contained, contributing to the vehicle’s efficiency and longevity.
Farm Equipment Repair
Farm machinery relies heavily on pumps for irrigation, spraying, and powering hydraulic systems. Durable and reliable pump seals help maintain the machinery's functionality, which is vital for agricultural productivity.
Structural Engineering
In structural engineering, pump seals are used in various applications like concrete pumps and drainage systems. Effective sealing ensures the integrity of structures and prevents water damage.
Conclusion: The Integral Role of Pump Seals in Business Success
In conclusion, pump seals serve as critical components that can significantly impact operational efficiency across various industries, from auto repair and farm equipment repair to structural engineering. Understanding their types, correct selection, and maintenance practices can lead to enhanced performance and reduced operational costs.
By taking the time to invest in quality pump seals and understanding their importance, businesses can enhance their reliability and sustainability, driving long-term success. For more insights and expert assistance, consider reaching out to professionals like Michael Smith Engineers, who specialize in providing high-quality engineering solutions tailored to your specific needs.